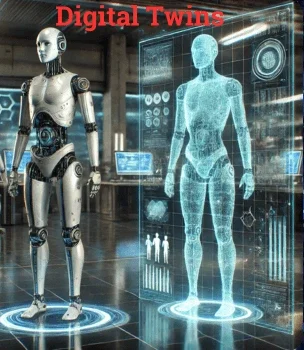
Digital twins are revolutionizing industries worldwide, and robotics is no exception. By creating a virtual representation of a physical robot, digital twins enable seamless simulation, monitoring, and optimization of robotic systems. This innovative approach bridges the gap between the physical and digital worlds, offering unparalleled insights and efficiency.
What Are Digital Twins?
A digital twin is a dynamic, real-time virtual replica of a physical system. In the context of robotics, it encompasses the physical robot, its environment, and associated data streams.
- Definition: Digital twins are more than just simulations; they are synchronized with real-world systems, reflecting changes in real time.
- Core Components: These include sensors, communication interfaces, and analytics tools that allow for data-driven decision-making.
- Importance in Robotics: Digital twins are critical for enhancing the design, deployment, and maintenance of robots across industries.
History and Evolution of Digital Twins
- Initial Concept: Coined by Dr. Michael Grieves in 2002, the idea initially focused on manufacturing.
- Adoption in Robotics: Over the past decade, advancements in IoT and AI have made digital twins indispensable in robotics.
- Future Potential: Emerging technologies, like 5G and edge computing, promise to expand their capabilities further.
Applications of Digital Twins in Robotics
Digital twins have found extensive applications in the robotics industry, driving innovation and efficiency across various domains.
Enhancing Robotic Design
Digital twins play a vital role in the conceptual and design phases of robotics.
- Prototyping: Virtual prototyping reduces the need for physical trials, saving time and cost.
- Testing: Simulation environments help test robot performance under diverse scenarios.
- Optimization: Engineers can fine-tune designs using data-driven insights from digital twins.
Improving Predictive Maintenance
Robotic systems often operate in demanding environments, making maintenance critical.
- Real-Time Monitoring: Sensors and IoT devices feed real-time data into the digital twin.
- Failure Prediction: AI-driven models analyze data to predict potential failures.
- Minimizing Downtime: Preventive measures can be implemented proactively, reducing operational disruptions.
Streamlining Operations in Manufacturing
Digital twins are integral to smart factories and Industry 4.0.
- Robotic Process Automation (RPA): They enable efficient monitoring and control of robotic processes.
- Resource Allocation: Digital twins help optimize the allocation of robots in assembly lines.
- Quality Control: They ensure consistent output by monitoring and adjusting robotic operations.
Training and Skill Development
Digital twins offer a safe and interactive way to train personnel.
- Operator Training: Virtual environments simulate real-world scenarios for hands-on learning.
- Collaborative Robots: Human-robot interaction can be tested and improved in a digital twin environment.
- Advanced Skills: Engineers can develop expertise in managing complex robotic systems.
Applications of Digital Twins Beyond Robotics
Digital twins, while transformative in robotics, have applications that extend across numerous fields, showcasing their versatility and impact.
Enhancing Healthcare Systems
Digital twins are redefining patient care and medical research.
- Personalized Medicine: Virtual models of patients allow for tailored treatments.
- Surgical Planning: Simulating procedures minimizes risks and enhances outcomes.
- Medical Device Development: Testing innovations virtually accelerates product readiness.
Revolutionizing Urban Planning
In smart cities, digital twins optimize infrastructure and resource management.
- Traffic Management: Simulations improve flow and reduce congestion.
- Energy Optimization: Monitoring systems predict and adjust consumption patterns.
- Disaster Preparedness: Real-time data aids in emergency response planning.
Advancing Industrial Operations
Manufacturing and supply chain processes benefit immensely from digital twins.
- Process Optimization: Virtual replicas identify inefficiencies and propose improvements.
- Supply Chain Transparency: Digital twins track goods and predict disruptions.
- Equipment Monitoring: Maintenance needs are identified before failures occur.
Supporting Environmental Sustainability
Digital twins contribute to ecological conservation and resource management.
- Climate Modeling: Simulations help predict environmental changes.
- Renewable Energy: Virtual systems optimize solar, wind, and hydroelectric setups.
- Biodiversity Preservation: Monitoring ecosystems ensures balanced conservation efforts.
Challenges and Future of Digital Twins in Robotics
Despite their benefits, implementing digital twins for robots presents challenges that need to be addressed.
Key Challenges
Data Integration
Integrating data from various sources can be complex and resource-intensive.
- Heterogeneous Systems: Robots often rely on diverse hardware and software components.
- Standardization Issues: Lack of industry standards can hinder interoperability.
- Data Accuracy: Ensuring real-time synchronization requires precise data management.
Scalability
Scaling digital twins across multiple robots or facilities can be demanding.
- Computational Requirements: High processing power is needed for real-time simulations.
- Network Infrastructure: Robust connectivity is crucial for large-scale implementations.
- Cost Constraints: Scaling can lead to significant investment in infrastructure and technology.
Security and Privacy
Digital twins are vulnerable to cyber threats due to their reliance on data.
- Cybersecurity Risks: Unauthorized access could compromise sensitive information.
- Data Privacy: Protecting proprietary data from breaches is critical.
- Compliance: Adhering to regulations like GDPR is essential.
The Future of Digital Twins for Robots
Emerging Technologies
- AI Integration: Advanced AI models will enhance predictive and analytical capabilities.
- 5G Connectivity: High-speed networks will improve real-time data transfer.
- Edge Computing: Localized processing will reduce latency and dependency on cloud services.
Expanding Use Cases
- Healthcare Robotics: Digital twins will play a pivotal role in surgical and assistive robots. (Leran more about healthcare robots).
- Agricultural Automation: Simulations will help optimize robotic systems for precision farming.
- Autonomous Vehicles: Digital twins will enhance the safety and efficiency of self-driving robots.
Global Collaboration
- Standardization Efforts: Industry-wide standards will facilitate seamless integration.
- Research and Development: Collaborative efforts will drive innovation and address current limitations.
- Education and Training: Digital twins will become essential tools in robotics education.
Conclusion:
Digital twins are transforming the robotics landscape, offering unprecedented opportunities for innovation and efficiency. By addressing current challenges and leveraging emerging technologies, digital twins will continue to unlock the full potential of robotic systems, shaping the future of industries worldwide.